Suggestions on advancing the technological progress of refractory production equipment in China
China's refractory industry after more than 60 years of construction and development, basically to meet the domestic steel, building materials, non-ferrous metals and other high-temperature industries at different times, China's refractory production accounts for about 40% of the world's total, has become the world's refractory Production and export power, is the goal of power forward. Industry emerged a large number of large enterprise groups, such as Liaoning blue and white, after the British, Henan Pu resistance, etc., its main production equipment are close to or reach the international advanced level. However, China's refractory production plant concentration is poor, uneven equipment, advanced and backward equipment coexist, the overall level of industry and developed countries compared to the industry there is still a considerable gap. Looking back at history, "concentrate" and "equipment (including furnace)" is the basis for the development of refractory materials, the development of circular economy, to achieve structural optimization, energy saving and emission reduction are inseparable from the refractory production equipment, technological progress. Looking forward to the "12 · 5", refractory production equipment technology development is still long way to go, it is recommended that the future work from the following aspects:
1. Refractory materials advanced production equipment to promote the use of
China's refractory production equipment technology after several generations of unremitting efforts, the development so far fruitful. New construction, the old production line transformation are constantly applying new production equipment. However, because China is the world recognized as a major producer of refractory materials, the old refractory plant occupies a large proportion of the old production equipment has generally lagged behind, and even some equipment facing the elimination. To become a powerful producer of refractory materials, the need to apply new production equipment technology as soon as possible. This requires the people of insight refractory people attach great importance to the equipment update and development, response to the development of new equipment has been continuously improved, the formation of serialization, regularly issued a list of industry equipment and equipment to promote new equipment, out of old equipment.
2. According to the refractory production needs of continuous innovation and development
Broken equipment
Broken crushing equipment generally there is a low efficiency, vibration and noise, wear-resistant materials and other issues. Improve the accuracy and quality of equipment manufacturing, research with high wear resistance of the material, to take effective methods to reduce vibration and reduce noise is the way to solve these problems.
Mixing equipment
A) Mixing equipment is one of the trends in the production of it with automatic weighing and automatic addition, discharge components to make it automated.
B) serialization and versatility of mixing equipment. Large, medium and small series of mixed design in some types of hybrid equipment has not yet formed. Some hybrid equipment does not yet have the versatile requirements, such as heating, cooling, pressurization, decompression, water and other additives to add and other functions.
C) In order to meet the production requirements of refractory new products, should be in line with the international advanced level, continue to develop new products to meet the production requirements of the plane, such as the shape of the spray equipment.
Forming equipment
Domestic friction presses in recent years has developed rapidly, has basically met the domestic refractory production needs. The composite friction press is the direction of the friction press, and its double-sided pressure, vacuum degassing, automatic detection, machine out of brick and from the feeding to the brick of the fully automated, in terms of reliability, stability also need Further improve the development of domestic and foreign large-tonnage hydraulic press and electric program-controlled screw press is one of the main issues of molding equipment; how to improve the isostatic pressing machine to suppress product output is the key issue; development of thin slab casting with a new generation of immersion The special production equipment of the water outlet is one of the urgent problems to be solved at present.
3. Energy - saving and clean production both the system technology research and development
We propose to improve the "refractory industrial furnace heat balance measurement calculation method unified provisions"; organization of scientific research strength, to develop a variety of refractory raw materials and products of "effective heat"; through research and actual calibration, the development of refractory industrial furnace "thermal efficiency "Mandatory standards, so as to promote the progress of energy conservation work; to determine the production of energy-saving rules, the system of refractory furnace design, production process energy-saving technologies, the development of large enterprises energy consumption targets; development of refractory enterprises dust emissions and furnace dust Discharge new standards, increase CO2, SO2, NOX emission standards.
Enterprise pollutants (furnace air pollutants, sewage, plant boundary environmental noise, etc.) should be all stable to meet national or local pollutant discharge standards. Product production enterprises production environment Environmental safety and health should meet the national or local standards.
4. Enhance the refractory sintering, fusing, nitriding three key technologies
New magnesite lighter kiln
For the light magnesium oxide reflex furnace has 70 to 80 years of history, but only roasting lumps, poor product quality, high energy consumption, poor working conditions, the urgent need to develop new magnesite light kiln. The new magnesite lighter kilns should consider emitting high concentrations of CO2 flue gas to create conditions for the economic recovery of CO2. It is recommended to design a new type of vertical kiln and rotary kiln with vertical preheater, and may consider the heat removal of the kiln to be silicon; the fine granular magnesite light The kiln can learn from the development of the fifth stage cyclone preheating suspension furnace to improve the solid gasification and thermal efficiency.
Re-burning magnesite shaft kiln
Re-burning magnesite with two or three magnesite ore, with solid fuel shaft kiln production, product prices lower. Re-burned magnesite shaft kiln more artificial use of materials, poor working conditions, dust pollution control difficult, to be completely managed.
Technology Renovation and Innovation of Electric Furnace
Three-phase electric arc furnace to "frit method" production of fused corundum and fused magnesia, its investment is small, construction fast, in recent years in China's development is very rapid, become the industry energy consumption, only southern Liaoning, Henan fuel consumption per year 2.5 million tons of standard coal, and product quality is not stable, serious pollution. Therefore, the production process of electrothermal furnace is imperative, in southern Liaoning, Jienan and other places to select the existing three-phase electric furnace pilot, and large-scale DC or inverter arc furnace research, to establish a model to promote.
Nitriding technology
Is currently vigorously developing nitrided or oxynitride composite refractory, which nitriding process and nitriding furnace is the key technology, focusing on the solution: ① by the carbon nitride nitrogen nitride products, need to solve the nitriding depth of more than 100mm nitriding process And nitriding furnace; ② The use of flicker combustion technology to synthesize AlN, Si3N4, MgAlON and SiAlON and other advanced nitride or oxynitride refractory materials, the need to develop synthetic technology and a new type of flash burning furnace.
5. Rationalization of fuel structure
The product after burning the fuel should not contaminate the product, or the degree of contamination within the allowable range of product quality. Therefore, the calcination of concentrate and firing high-quality products, must adhere to the use of low-ash liquid fuel or high calorific value of gas fuel.
As China's unit of gross national product occupies fuel is too high, resulting in fuel shortage; relatively speaking, coal, less fuel, blast furnace, coke oven and converter gas shortage. In recent years, natural gas, coalbed methane and other clean fuels can be supplied to refractory enterprises, should be promoted to ensure supply. From the actual situation in China, the key work carried out: ① the development of efficient pulverized coal preparation equipment, the application of anthracite as a rotary kiln fuel; ② comprehensive utilization of coal resources, the use of two gas furnace gas as refractory furnace fuel; Taking into account the use of gaseous fuels and solid fuels, high calorific value fuels and low calorific value fuels and oxygen-enriched two or three burner technology.
6. Promote refractory furnace with oxygen-rich combustion technology
With air combustion, a lot of heat is taken away by the nitrogen in the air, accounting for more than 30% of the total heat, resulting in low heat utilization, high temperature calcination difficult and unstable. When the combustion temperature is> 1300 ° C, the amount of NOx produced increases exponentially with temperature. In high temperature, ultra-high temperature conditions, the smoke containing high NOx, increasing the difficulty of governance. Oxygen-enriched air in the O2 content is generally 22% to 30%. At present, China's small-scale oxygen technology progress is relatively large, the use of oxygen-rich combustion is economically viable, therefore, to promote refractory furnace using oxygen-rich combustion technology, the conditions are ripe.
7. Improve the level of automatic control of the furnace
China's refractory industrial furnace overall low level of automation control, a considerable part of the furnace on the operator's dependence is very large, directly related to the furnace consumption and yield, it is necessary to gradually increase the level of control.
Furnace automation control is the key to solve a temperature measurement instrument, followed by data transmission and intelligent control. The temperature and pressure of the furnace are monitored, and the operation trend is forecasted and adjusted to realize the digital operation of the furnace, so as to achieve the goal of improving the yield and reducing the energy consumption and increasing the savings. Furnace intelligent control is the direction of the development of modern kiln, conditional enterprises can modern refractory furnace design and production of the entire production simulation software.
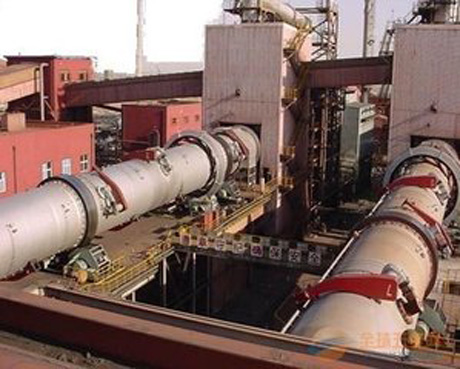
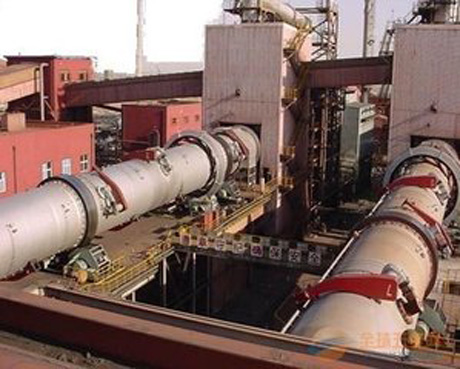
Products Categories
Refractory Knowledge
- What Are The Properties Of Glass Refractory? 2015-09-24 19:51:06
- High alumina bricks have performance advantages 2018-05-21 09:57:40
- Application Effect of Energy Saving Material Aluminum Silicat 2018-03-09 15:00:30
- Zirconium corundum mullite castable 2019-01-02 17:18:22
- Billet Cracking Of Zircon Brick 2015-09-14 22:52:31
- Insulation brick selection and function 2018-04-11 15:37:31
Contact Us
- Email:sales@sunriserefr.com
- MSN:hksunrise@hotmail.com
- Skype:tkfanyi / zzty371
- Mobile:+86-13015506292
- Tel:+86-371-63838939
- Fax:+86-371-63835539