Do you know how to prepare sintered zircon mullite bricks?
A method for preparing a sintered zirconium mullite brick, which comprises batching, molding, and firing.
I. Ingredients: The raw materials for the sintering of zirconium mullite bricks are mullite clinker, zirconium mullite clinker and binder. The chemical weight composition of the zirconium mullite clinker is: Al2O335-55% SiO210-266% ZrO 216~38% balance is a conventional impurity.
The raw materials for the preparation of zirconium mullite clinker are zircon and alumina, and the synthesis temperature thereof is 1600 to 1700 °C.
When the ingredients are prepared, the zirconium mullite clinker is a powder having a particle diameter of less than 0.088 mm, and the mullite clinker is pulverized into particles of various levels, and the particle size and the weight gradation are: particle diameter d<0.04 mm, 20-50% 0.04 ≤ d < 0.1 mm, 5 to 15% 0.1 ≤ d < 0.5 mm, 5 to 15% 0.5 ≤ d < 1 mm, 20 to 30% 1 ≤ d < 3.5 mm, 20 to 30%.
Second, molding:
1. Mixing: The raw materials are matched according to the ratio. The coarse particles and the bonding agent are first added in the mixing machine. The bonding agent may be an organic binder, an inorganic binder, or a composite combination of the two. Agents, such as polyvinyl alcohol solution, plastic clay, etc., after a little mixing, add fine powder and mix.
2, stale: the mixed materials are stale 12 or more.
3. Molding: It can be formed by friction press or hydraulic press, and the corresponding mold can be selected for various brick types.
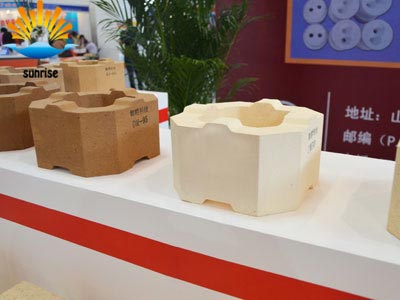
4. Drying: The green body is dried to less than 2% moisture and ready for cooking.
3. Firing: The dried body is fired at a firing temperature of 1600 to 1700 °C.
The sintered mullite brick of Sunrise refractory is composed of a needle-like mullite structure network and a complex phase structure composed of oblique zircon crystals. The oblique zircon grains are evenly distributed in the mullite network structure, which constitutes The anti-erosion body of the material, the composite binder activates the surface of the particles, promotes the sintering reaction, and can generate a new crystal phase, improve and improve the performance of the grain boundary. Such a structure makes the refractory material have high softness, high refractoriness and high resistance. Corrosive and thermal shock resistance. At the same time, the microcracks generated at the grain boundaries during the zircon transformation have a toughening effect, which further improves the thermal stability of the refractory. The refractory brick has a long service life and generally lasts for more than 6 years.
After testing, the bulk density of the refractory brick is greater than 2.78 g/cm3, the apparent porosity is less than 16%, the normal temperature compressive strength is greater than 86 MPa, the load softening temperature is greater than 1600 ° C, and the thermal stability is greater than 15 times.
Products Categories
Refractory Knowledge
- What Are The Properties Of Glass Refractory? 2015-09-24 19:51:06
- Billet Cracking Of Zircon Brick 2015-09-14 22:52:31
- Glass furnace structure and various parts of refractory mater 2018-01-15 09:30:52
- Application Effect of Energy Saving Material Aluminum Silicat 2018-03-09 15:00:30
- High alumina bricks have performance advantages 2018-05-21 09:57:40
- Insulation brick selection and function 2018-04-11 15:37:31
Contact Us
- Email:sales@sunriserefr.com
- MSN:hksunrise@hotmail.com
- Skype:tkfanyi / zzty371
- Mobile:+86-13015506292
- Tel:+86-371-63838939
- Fax:+86-371-63835539