Performance and use of insulation refractories
Insulating refractories of different materials have different operating temperatures and performance characteristics, and ultimately determine their use. The refractory material that we will focus on today is the insulation board.
The heat insulation board is a kind of non-burning product, which is composed of refractory fiber material, refractory raw material, binder and admixture, and is an important variety of thermal insulation refractory materials. The insulation board is divided into silicon, magnesia, forsterite, aluminum silicate and floating beads according to the material; this material is characterized by low thermal conductivity, low density and good corrosion resistance, and is mainly used in ingots. The hatch and the continuous casting tundish and the like are therefore referred to as the tundish insulation plate and the mold insulation plate, respectively. The tundish insulation board is divided into a wall panel, a bottom plate and an impact plate, and the performance differs depending on the location of use.
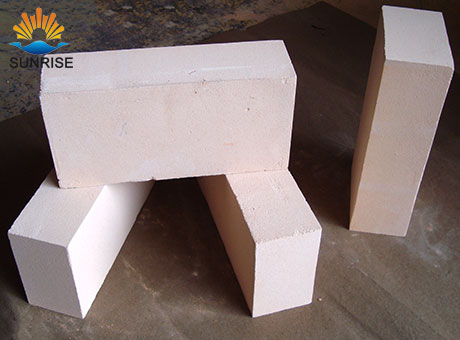
Insulation refractories can only be used for thermal insulation without exceeding their maximum allowable temperature. Therefore, according to the energy-saving purpose and requirements of the kiln, structural characteristics, working conditions, and service life requirements, the thermal insulation refractory materials should be reasonably selected. For example, in a copper reverberatory furnace, the non-working layer can be constructed of high-strength lightweight refractory clay bricks or refractory fibers, and the lining can only be built with heavy refractory bricks due to erosion by slag and intense flame scouring. Do not use lightweight, porous insulation materials. The thermal insulation refractory layer is applied to the outer surface or the hot surface of the furnace wall, and the thermal insulation effect is also different. Generally, the continuous operation of the kiln is more reasonable by external insulation, that is, the work is lined with dense refractory bricks, while the non-working layer is made of lightweight bricks, which can significantly reduce heat loss, and the energy saving rate is over 10%. The strength and stability of the furnace wall are guaranteed. In the intermittent operation of the kiln, if the external heat insulation method is adopted, although the heat loss is reduced, the increase in the heat storage loss sometimes exceeds the heat loss, so the internal heat insulation is often used to reduce the heat storage loss. Some of the furnace walls of non-melting furnaces are even made of lightweight bricks, which has significant energy-saving effects.
If you are interested in our refractory materials, or need other refractory bricks, you can contact Sunrise Refractory Company, we will get in touch with you in the first time.
Products Categories
Refractory Knowledge
- Glass furnace structure and various parts of refractory mater 2018-01-15 09:30:52
- What are the characteristics of Refractory Brick? 2016-09-30 17:58:32
- Zirconium corundum mullite castable 2019-01-02 17:18:22
- Insulation brick selection and function 2018-04-11 15:37:31
- High alumina bricks have performance advantages 2018-05-21 09:57:40
- Billet Cracking Of Zircon Brick 2015-09-14 22:52:31
Contact Us
- Email:sales@sunriserefr.com
- MSN:hksunrise@hotmail.com
- Skype:tkfanyi / zzty371
- Mobile:+86-13015506292
- Tel:+86-371-63838939
- Fax:+86-371-63835539