Brief analysis of zircon mullite brick and its production process
What is zircon mullite?
In order to further improve the mullite's resistance to chemical attack, thermal shock and reduce the expansion coefficient, zrO can be introduced in the Al20-S0z system to achieve the purpose of improving the mullite structure. The mullite containing zirconium dioxide is zirconium Mullite. Zircon mullite is generally produced by electrofusion.
ZrO2 is introduced into mullite and has two functions: 1. forming a solid solution, activating the crystal lattice, and forming vacancies: it can play a role in promoting sintering: using the phase change additive mechanism of ZrO. Improved high-temperature mechanical properties. When the mass fraction of zrO; is between 15% and 30% 2, it is mainly stress-induced phase transition increaser: Z0; when it is greater than 30%, it is mainly microcrack toughening.
Zircon mullite is mainly used in the new type of cast steel slides, continuous casting sizing, long nozzles and key parts of glass furnaces.
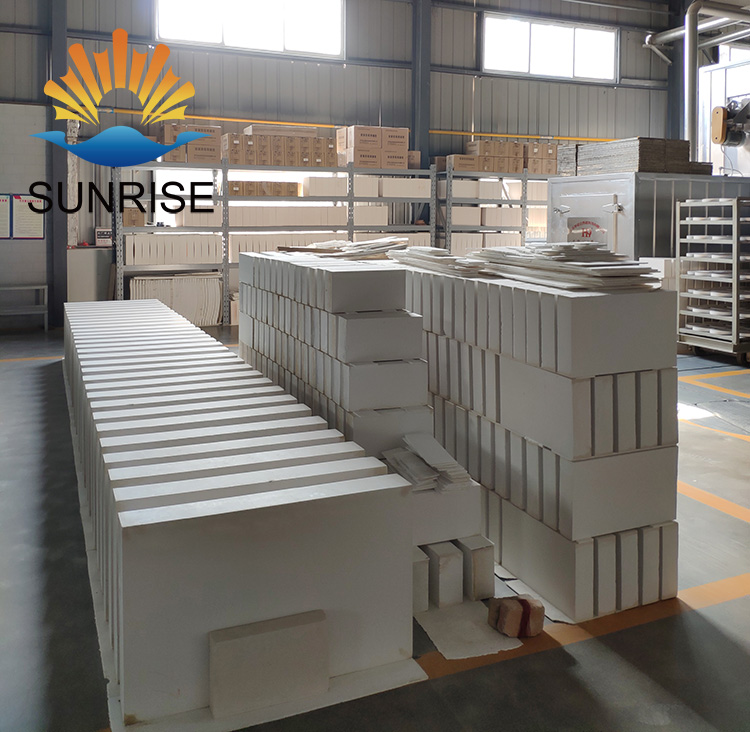
Production process of fault mullite
Zircon mullite is a mullite-zirconia composite material. Its high-temperature mechanical properties such as strength, creep resistance and thermal shock resistance, as well as corrosion resistance are better than single-phase mullite materials. Therefore, it is more versatile, in addition to the occasions used for mullite products, it is also used in skateboards, glass kiln villages and other parts. Chemical composition of raw materials and production process: Zircon mullite clinker is synthesized by sintering kyanite concentrate as the main raw material, adding industrial alumina and spodumene.
The test adopts the following process flow:
fine grinding of raw materials → batching → common mixing grinding →> mud preparation → blank making → drying> firing → clinker → detection
The particle size requirements of the raw materials for co-milling: less than 15 μm accounts for more than 70%. The results determined that: less than 15 μm accounted for 70%, of which less than 5 μm accounted for 40%. The fineness of the raw material for the synthesis of mullite is an important parameter. The molding pressure is 200MPa; the bulk density of the green body is 2.15 ~ 2.35g / cm3; the firing temperature is 1700C, 4h.
Products Categories
Refractory Knowledge
- What Are The Properties Of Glass Refractory? 2015-09-24 19:51:06
- What are the characteristics of Refractory Brick? 2016-09-30 17:58:32
- Suggestions on advancing the technological progress of refrac 2017-06-19 10:33:27
- Billet Cracking Of Zircon Brick 2015-09-14 22:52:31
- Hot Sale Zircon Mullite Bricks Factory Directly Supply 2019-11-27 15:39:50
- Glass furnace structure and various parts of refractory mater 2018-01-15 09:30:52
Contact Us
- Email:sales@sunriserefr.com
- MSN:hksunrise@hotmail.com
- Skype:tkfanyi / zzty371
- Mobile:+86-13015506292
- Tel:+86-371-63838939
- Fax:+86-371-63835539