Introduction to the production process of zircon brick
In industrial production, in order to reduce costs and improve economic benefits, cheap and high-quality zircon raw materials have been widely used to make sintered zircon bricks. Zircon (ZrSiO4) crystals are tetragonal, and their crystal form is usually a prism. Colors are red, purple, brown, yellow and gray. The theoretical composition of zircon is ZrO2: 67.23%, and SiO2: 32.77%. Zircon has a melting point of 2420, a density of 4.6 to 4.7 g / cm3, and a Mohs hardness of 7.5.
The zircon raw materials used to make zircon bricks require a purity of 98% to 99%. The content of ZrO2 should be greater than 63%, and the lower the content of impurities, the better. In the production of products, the pure zircon fine powder is first pressed into compacts, then calcined at about 1600, then crushed, shaped and finally fired. Zircon began to dissociate slowly from 1540 and rapidly dissociated from 1750. By 1870, the amount of dissociation reached 95%. The dissociation products are monoclinic zirconia and silica glass. As dissociation progresses, swelling variants of zirconia become increasingly important.
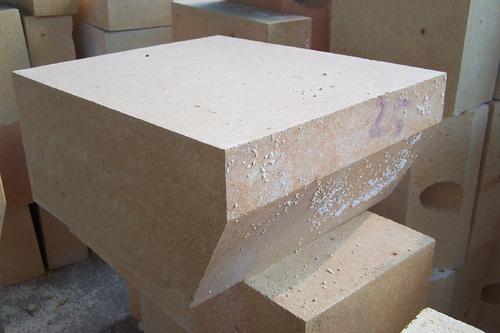
Due to this function, the final firing temperature of the zircon brick does not exceed 1600. According to the volume change of the zircon green body during the firing process, the heating rate below 600 should be reduced to facilitate the removal of water and organic substances from the green body. Body; between 600 and 1200, sintering has not started and the temperature may rise. accelerate. Between 1200 and 1500, the body contracts violently, so the heating rate should be slower. When molding zircon bricks, appropriate cosolvents and mineralizers need to be added. Examples of ingredients are: 40% molten zircon particles, 40% zircon sand, 20% zircon powder and a small amount of fluoride. Using dextrin as a binder, it was molded under high pressure.
Products Categories
Refractory Knowledge
- What are the characteristics of Refractory Brick? 2016-09-30 17:58:32
- Insulation brick selection and function 2018-04-11 15:37:31
- Application Effect of Energy Saving Material Aluminum Silicat 2018-03-09 15:00:30
- What Are The Properties Of Glass Refractory? 2015-09-24 19:51:06
- Suggestions on advancing the technological progress of refrac 2017-06-19 10:33:27
- Billet Cracking Of Zircon Brick 2015-09-14 22:52:31
Contact Us
- Email:sales@sunriserefr.com
- MSN:hksunrise@hotmail.com
- Skype:tkfanyi / zzty371
- Mobile:+86-13015506292
- Tel:+86-371-63838939
- Fax:+86-371-63835539