Production and classification of mullite bricks
High alumina refractory with mullite (3Al2O3 · 2SiO2) as the main crystal phase. Generally the alumina content is between 65% and 75%. Mineral composition In addition to mullite, the lower alumina contains a small amount of glass phase and cristobalite;
Those with higher alumina also contained a small amount of corundum. High fire resistance, up to 1790 ℃. Load softening start temperature is 1600 ~ 1700 ℃. The compressive strength at room temperature is 70 ~ 260MPa. Good thermal shock resistance.
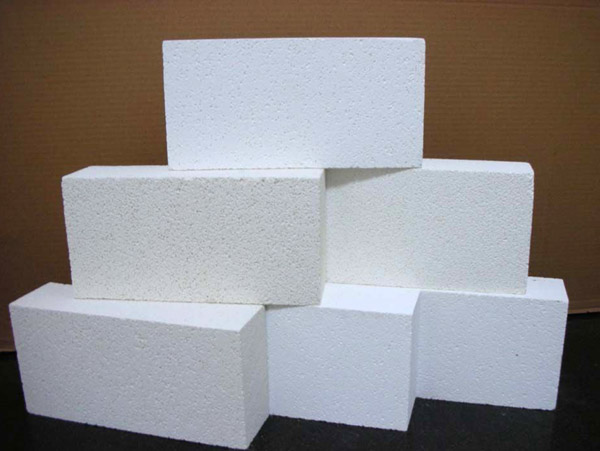
There are two types of sintered mullite bricks and fused mullite bricks.
The sintered mullite brick is made of high alumina bauxite clinker, and a small amount of clay or raw alumina is added as a binder, and then formed and fired. The fused mullite brick is made of high alumina, industrial alumina and refractory clay, and is added with charcoal or coke fine particles as a reducing agent. After molding, it is manufactured by reduction electrofusion method.
The fused mullite crystals are larger than the sintered mullite and have better thermal shock resistance than the sintered products. Their high temperature performance is mainly determined by the alumina content and the uniformity of the mullite phase and glass distribution. Mainly used in hot blast stove top, blast furnace body and bottom, glass melting furnace heat storage chamber, ceramic sintering kiln, dead angle lining of petroleum cracking system, etc.
If you are interested in our fused azs bricks, or need other types of refractory materials, please contact our Tianyang Refractory Group, we will definitely provide you with the best quality refractory materials and the most reasonable quotation.
Those with higher alumina also contained a small amount of corundum. High fire resistance, up to 1790 ℃. Load softening start temperature is 1600 ~ 1700 ℃. The compressive strength at room temperature is 70 ~ 260MPa. Good thermal shock resistance.
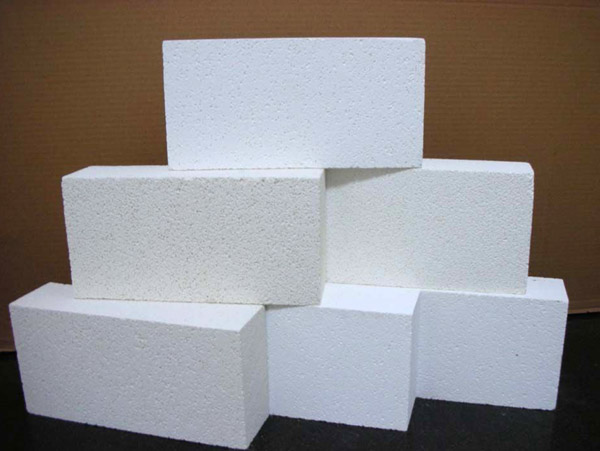
There are two types of sintered mullite bricks and fused mullite bricks.
The sintered mullite brick is made of high alumina bauxite clinker, and a small amount of clay or raw alumina is added as a binder, and then formed and fired. The fused mullite brick is made of high alumina, industrial alumina and refractory clay, and is added with charcoal or coke fine particles as a reducing agent. After molding, it is manufactured by reduction electrofusion method.
The fused mullite crystals are larger than the sintered mullite and have better thermal shock resistance than the sintered products. Their high temperature performance is mainly determined by the alumina content and the uniformity of the mullite phase and glass distribution. Mainly used in hot blast stove top, blast furnace body and bottom, glass melting furnace heat storage chamber, ceramic sintering kiln, dead angle lining of petroleum cracking system, etc.
If you are interested in our fused azs bricks, or need other types of refractory materials, please contact our Tianyang Refractory Group, we will definitely provide you with the best quality refractory materials and the most reasonable quotation.
Products Categories
Refractory Knowledge
- High alumina bricks have performance advantages 2018-05-21 09:57:40
- Hot Sale Zircon Mullite Bricks Factory Directly Supply 2019-11-27 15:39:50
- Billet Cracking Of Zircon Brick 2015-09-14 22:52:31
- What are the characteristics of Refractory Brick? 2016-09-30 17:58:32
- Suggestions on advancing the technological progress of refrac 2017-06-19 10:33:27
- What Are The Properties Of Glass Refractory? 2015-09-24 19:51:06
Contact Us
- Email:sales@sunriserefr.com
- MSN:hksunrise@hotmail.com
- Skype:tkfanyi / zzty371
- Mobile:+86-13015506292
- Tel:+86-371-63838939
- Fax:+86-371-63835539