Introduction to the use of common acid-resistant castables
We know that as a widely used refractory material, acid-resistant refractory castables can be used as anti-corrosive flue and chimney linings, acid storage tanks, pickling tank linings, nitric acid purifying tower linings and other acidic high temperature Gas eroded container linings, etc. Aggregates used to configure acid and refractory castables are mainly silica, cast stone, wax stone, andesite, and diabase.
Acid-resistant castable is an acid-resistant material combined with water glass. Water-glass combined can reduce the amount of Na2O and increase acid resistance. In general, it can resist acid corrosion at 800-1200 ℃; but acid-resistant castables are not resistant to alkali, hot phosphoric acid, hydrofluoric acid, and fatty acid. The acid resistance is related to the aggregate and powder used. Sometimes the raw materials of different substrates are selected according to different situations and different use sites.
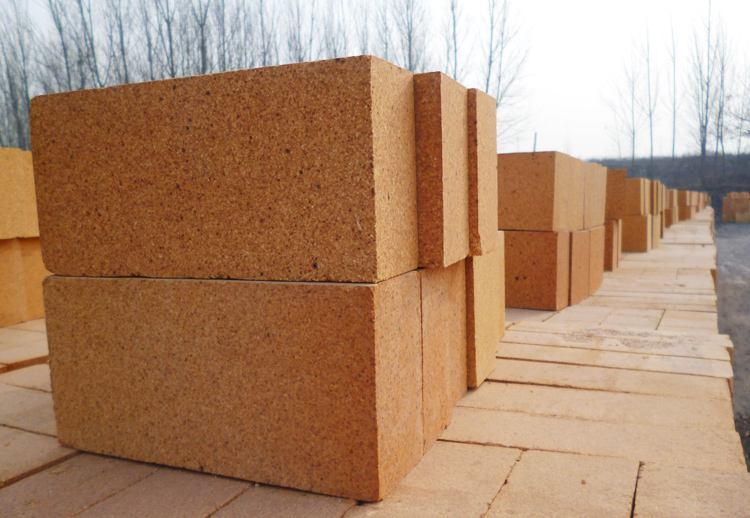
Acid-resistant castables have better strength and stability when immersed in acid. Generally, the compressive strength increases with the immersion time. The acid-resistant castables are alternately anticorrosive, and therefore the anticorrosive performance is greatly improved. Because the acid-resistant castables have high anticorrosive properties, they can not only meet the anticorrosion requirements in acid corrosion environments, but also meet the fatigue requirements of alternating performance. It also has a long survival time under extremely harsh environments, as well as the shrinkage, hardness, toughness, wear resistance, and high temperature resistance of the acid-resistant castable itself, which also lays a solid foundation for corrosion protection in extremely harsh acidic environments.
Acid and refractory castables are mainly used as corrosion-resistant flue and chimney linings, acid storage tanks, pickling tank linings, nitric acid concentration tower linings, acid recovery furnace linings and other container linings corroded by acidic high-temperature gases. Wait. The construction temperature of the acid-resistant and refractory castable should be above 15 ℃. Try not to construct in the rainy season. Add the material to the mixer during the construction, and stir well. The aggregate is first powdered, and then the binder. The mixed material must be used up within 30 minutes. In particular, it should be noted that during the construction process, powder and some binding agents cannot be added. If you find that the cement has hardened, discard it.
The acid resistance (weight method,%) of several commonly used raw materials is: cast stone 98%, silica greater than 97%, clay clinker 92% to 97%, wax stone 92 to 96%, andesite is greater than 94%. Which raw materials are used depends on the conditions of use. However, when using silica, it is necessary to pay attention to the polycrystalline transformation of quartz during heating, which will cause volume change (expansion) during the transformation. Therefore, it is best to use waste silica bricks instead of some silica raw materials as aggregates and configure the powder of this castable. Silica powder, cast stone powder, porcelain powder, high siliceous clay clinker powder, etc. are mainly used. Among them, cast stone powder is more acid-resistant powder.
The binder water glass should use a water glass with a higher M to reduce the amount of Na2O brought into the water glass and improve the acid resistance. Generally, a water glass solution with a modulus of 2.6-3.2 and a density of 1.38-142, g / cm3 is used. There are many compounds that can be used as water glass coagulants, including fluorine-containing compounds (such as alkali metal salts of fluosilicic acid, fluoboric acid, fluotitanic acid), esters, and acids
Acid-resistant castable is an acid-resistant material combined with water glass. Water-glass combined can reduce the amount of Na2O and increase acid resistance. In general, it can resist acid corrosion at 800-1200 ℃; but acid-resistant castables are not resistant to alkali, hot phosphoric acid, hydrofluoric acid, and fatty acid. The acid resistance is related to the aggregate and powder used. Sometimes the raw materials of different substrates are selected according to different situations and different use sites.
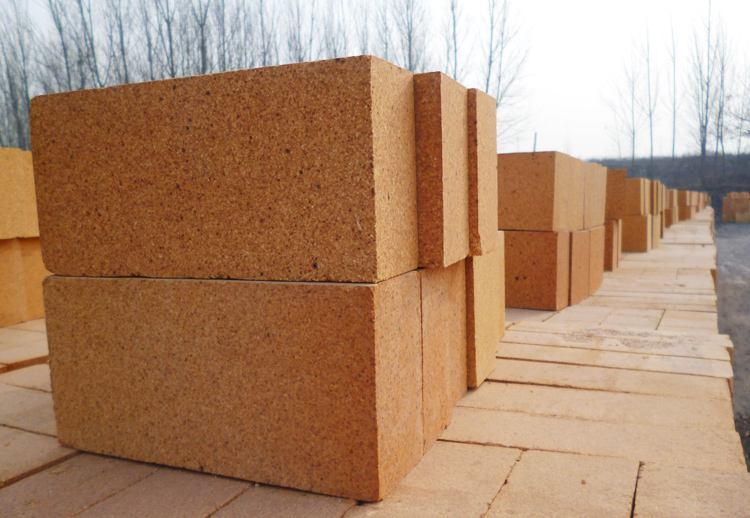
Acid-resistant castables have better strength and stability when immersed in acid. Generally, the compressive strength increases with the immersion time. The acid-resistant castables are alternately anticorrosive, and therefore the anticorrosive performance is greatly improved. Because the acid-resistant castables have high anticorrosive properties, they can not only meet the anticorrosion requirements in acid corrosion environments, but also meet the fatigue requirements of alternating performance. It also has a long survival time under extremely harsh environments, as well as the shrinkage, hardness, toughness, wear resistance, and high temperature resistance of the acid-resistant castable itself, which also lays a solid foundation for corrosion protection in extremely harsh acidic environments.
Acid and refractory castables are mainly used as corrosion-resistant flue and chimney linings, acid storage tanks, pickling tank linings, nitric acid concentration tower linings, acid recovery furnace linings and other container linings corroded by acidic high-temperature gases. Wait. The construction temperature of the acid-resistant and refractory castable should be above 15 ℃. Try not to construct in the rainy season. Add the material to the mixer during the construction, and stir well. The aggregate is first powdered, and then the binder. The mixed material must be used up within 30 minutes. In particular, it should be noted that during the construction process, powder and some binding agents cannot be added. If you find that the cement has hardened, discard it.
The acid resistance (weight method,%) of several commonly used raw materials is: cast stone 98%, silica greater than 97%, clay clinker 92% to 97%, wax stone 92 to 96%, andesite is greater than 94%. Which raw materials are used depends on the conditions of use. However, when using silica, it is necessary to pay attention to the polycrystalline transformation of quartz during heating, which will cause volume change (expansion) during the transformation. Therefore, it is best to use waste silica bricks instead of some silica raw materials as aggregates and configure the powder of this castable. Silica powder, cast stone powder, porcelain powder, high siliceous clay clinker powder, etc. are mainly used. Among them, cast stone powder is more acid-resistant powder.
The binder water glass should use a water glass with a higher M to reduce the amount of Na2O brought into the water glass and improve the acid resistance. Generally, a water glass solution with a modulus of 2.6-3.2 and a density of 1.38-142, g / cm3 is used. There are many compounds that can be used as water glass coagulants, including fluorine-containing compounds (such as alkali metal salts of fluosilicic acid, fluoboric acid, fluotitanic acid), esters, and acids
Products Categories
Refractory Knowledge
- Insulation brick selection and function 2018-04-11 15:37:31
- Application Effect of Energy Saving Material Aluminum Silicat 2018-03-09 15:00:30
- Glass furnace structure and various parts of refractory mater 2018-01-15 09:30:52
- Suggestions on advancing the technological progress of refrac 2017-06-19 10:33:27
- What are the characteristics of Refractory Brick? 2016-09-30 17:58:32
- Billet Cracking Of Zircon Brick 2015-09-14 22:52:31
Contact Us
- Email:sales@sunriserefr.com
- MSN:hksunrise@hotmail.com
- Skype:tkfanyi / zzty371
- Mobile:+86-13015506292
- Tel:+86-371-63838939
- Fax:+86-371-63835539